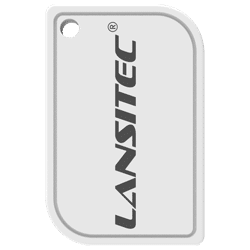
i3+ Portable Bluetooth Beacon
The i3+ Bluetooth Smart Finder Tag is a small and effective option for individuals wanting to improve asset tracking, personnel management, and resource optimization. If you’re handling a vast range of stock or simply organizing personal belongings, this tool is created to ease your issues with little to no trouble.
Executive Summary i3+ Bluetooth Smart Finder Tag
This case study analyzes how the i3+ Bluetooth Smart Finder Tag was used in a medium-sized delivery company to tackle operational challenges like monitoring delivery staff, tracking time at delivery sites, and automating attendance and shift scheduling. The company encountered challenges in optimizing delivery routes, ensuring deliveries were made on time, and keeping accurate records of personnel attendance.
In order to address these issues, the i3+ Bluetooth Smart Finder Tag was implemented as a small, keychain-attached tool that delivery personnel carried. This label, which has Bluetooth 5.0 technology and a 3D accelerometer, allows for instant tracking of location, automatic time recording at stops, and easy attendance control. Incorporating the tags into the company’s current delivery management system offered a strong, easy-to-manage method for improving operational monitoring and effectiveness.
The introduction of the i3+ tag resulted in notable enhancements in delivery route compliance, leading to a 15% decrease in overall delivery durations. Time spent at delivery sites became more reliable, as outliers decreased by 20%, resulting in improved time management. Moreover, automating attendance and shift management lowered administrative mistakes by 30% and removed the requirement for manual timekeeping. These outcomes enhanced the performance of delivery personnel by increasing efficiency, which in turn improved customer satisfaction and operational effectiveness.
Introduction
Background of the Delivery Company and the Operational Challenges
The logistics provider discussed in this case study is a medium-sized delivery company that focuses on offering last-mile delivery services in urban and suburban regions. The business employs 50 delivery staff who manage numerous daily deliveries. Although the company is known for its dependable service, it has encountered numerous operational obstacles that have impacted its effectiveness and overall success.
Main obstacles involve problems in monitoring the current whereabouts of delivery staff, resulting in ineffective route planning and late deliveries. Moreover, the amount of time required at different delivery destinations varied greatly, resulting in inconsistencies in delivery schedules and decreased efficiency. Furthermore, the manual recording of attendance and shift management led to errors and inefficiencies, increasing complications in payroll processing and shift planning.
Overview of the i3+ Bluetooth Smart Finder Tag and Its Potential Benefits
To address these challenges, the company decided to implement the i3+ Bluetooth Smart Finder Tag, a compact and portable tracking device designed to assist in asset and personnel management. The i3+ tag offers several key features that make it ideal for this use case:
- Bluetooth 5.0 Connectivity: Ensures reliable long-range communication (up to 150 meters) with minimal power consumption.
- 3D Accelerometer: Detects movement, allowing for tracking of personnel activity and time spent at specific locations.
- Compact Design: The small size and lightweight nature (6.2 g) make it easy for personnel to carry the tag as part of their keychain or attached to their uniform.
- Long Battery Life: The tag’s battery life of up to 765 days ensures continuous operation without frequent maintenance.
The i3+ tag’s capabilities allow for real-time tracking of delivery personnel, automated logging of time spent at delivery locations, and seamless attendance and shift management. By integrating the tag into their operations, the company aimed to enhance route efficiency, improve time management, and reduce administrative overhead.
Objectives of the Case Study
The primary objectives of this case study are as follows:
- Evaluate the impact of the i3+ Bluetooth Smart Finder Tag on tracking delivery personnel’s routes: Analyze how the real-time location tracking feature can improve route optimization and delivery times.
- Assess the effectiveness of the i3+ tag in monitoring time spent at delivery locations: Determine if the tag can help standardize the time spent at delivery stops, leading to more consistent and efficient deliveries.
- Examine the benefits of automating attendance and shift management using the i3+ tag: Measure the reduction in administrative errors and the efficiency gained from automated attendance tracking.
This case study aims to demonstrate how the i3+ Bluetooth Smart Finder Tag can address key operational challenges faced by the delivery company and provide actionable insights for further improving their logistics operations.
Problem Statement
The delivery company in this case study faced three primary operational challenges that impacted its efficiency, service quality, and overall performance. These challenges are detailed below:
Challenges in Tracking Delivery Personnel on Their Routes
One major obstacle was the difficulty in accurately monitoring the current whereabouts of delivery staff in real-time. Managers found it challenging to monitor route adherence, reroute personnel effectively, or give customers precise delivery time estimates due to the lack of accurate tracking. The absence of visibility frequently led to delayed deliveries, ineffective route handling, and an incapacity to react promptly to on-site problems like traffic or unforeseen delays.
Issues Related to Time Management at Delivery Locations
Another critical issue was the inconsistent amount of time delivery personnel spent at each stop. In some cases, personnel would spend more time than necessary at a single location, causing delays in subsequent deliveries. Conversely, rushing through stops sometimes led to errors such as incorrect package handling or missed deliveries. The variability in time spent at delivery points created inefficiencies that disrupted the overall delivery schedule and reduced the company’s ability to maintain consistent service levels.
Difficulties in Managing Attendance and Shifts for Delivery Personnel
Dealing with attendance and shifts manually had its own difficulties to overcome. Delivery workers had to use old-fashioned methods to record their work hours, leading to potential mistakes, forgetfulness, and discrepancies. This frequently resulted in incorrect attendance logs, causing issues with payroll and hindering efficient shift management. The absence of automation in attendance monitoring resulted in higher administrative responsibilities for managers, shifting their focus away from essential tasks connected to delivery operations.
Solution Overview
Details of the i3+ Bluetooth Smart Finder Tag and Its Key Features
The i3+ Bluetooth Smart Finder Tag is a compact, portable tracking device designed to assist with asset and personnel management. It is equipped with several key features that make it particularly suited for addressing the operational challenges faced by the delivery company:
- Bluetooth 5.0 Connectivity: Provides reliable long-range communication with a transmission distance of up to 150 meters, enabling accurate real-time location tracking.
- 3D Accelerometer: Detects and reports movement, allowing for monitoring of activity levels and time spent at specific locations.
- Compact and Lightweight Design: With dimensions of 38x25x5 mm and a weight of just 6.2 g, the tag is small enough to be unobtrusively attached to a keychain or uniform, ensuring it does not interfere with daily operations.
- Long Battery Life: The tag uses a CR2032 battery with a capacity of 230 mAh, offering an average battery life of 765 days, reducing the need for frequent replacements and maintenance.
These features enable the i3+ tag to provide continuous, reliable tracking and data collection without requiring significant changes to existing workflows.
Explanation of How the Tags Were Deployed
To address the challenges identified, the i3+ Bluetooth Smart Finder Tags were deployed across the delivery fleet. Each delivery personnel were assigned a tag, which was securely attached to their keychain or uniform. The small size and lightweight nature of the tag ensured that it did not hinder their movement or daily tasks. The tags continuously broadcast their location data, utilizing the Bluetooth 5.0 protocol to communicate with receivers placed strategically along delivery routes and at key locations such as the depot and delivery destinations.
Integration with the Delivery Management System
The i3+ tags were integrated with the company’s existing delivery management system, enabling seamless real-time tracking and data collection. The system was configured to receive the Bluetooth signals from the tags, allowing managers to monitor the location of each delivery personnel on a live map. This integration provided several key functionalities:
- Real-Time Route Tracking: Managers can monitor delivery personnel’s location in real-time, ensure they are sticking to the intended route, and make real-time adjustments to improve efficiency.
- Time Management at Delivery Locations: The system was made to track the duration delivery personnel spent at each stop to identify inefficiencies and establish consistent delivery times.
- Automated Attendance and Shift Management: The system automatically logged depot entry and exit times for personnel, simplifying attendance monitoring and shift scheduling, and decreasing reliance on manual timekeeping.
By adding the i3+ Bluetooth Smart Finder Tag, the company enhanced its delivery operations, reduced inefficiencies, and boosted productivity. Integration with the delivery management system guaranteed that all necessary information was collected and used for making informed choices that enhanced operational efficiency and customer contentment.
Implementation Process
Preparation Phase
The implementation of the i3+ Bluetooth Smart Finder Tag began with a thorough preparation phase to ensure a smooth rollout. Key activities included:
- Selection of Participants: The company selected 20 delivery personnel from different routes, covering a mix of urban and suburban areas. These participants were chosen based on their diverse delivery patterns, ensuring the case study would cover various operational scenarios.
- Installation of Tags: Each selected participant received an i3+ Bluetooth Smart Finder Tag. The tags were attached to their keychains, ensuring they would carry the device with them throughout their shifts. The compact design and lightweight nature of the tags meant they did not interfere with the delivery personnel’s daily activities.
Training: The company conducted a brief training session for the selected delivery personnel and their managers. This training covered the purpose of the tags, how they would be used in daily operations, and the importance of carrying the tags consistently. Additionally, the managers were trained on how to use the delivery management system to monitor the data generated by the tags, track personnel, and manage shifts.
Implementation Phase
Once the preparation was complete, the solution was rolled out in the following phases:
- Tracking of Delivery Personnel on Their Routes:
- The i3+ tags began transmitting real-time location data via Bluetooth to the company’s delivery management system. The system provided managers with a live map displaying the location of each tagged delivery personnel. This enabled better route management, allowing for adjustments based on traffic conditions or other factors that could affect delivery times.
- The system also tracked route adherence, ensuring that delivery personnel followed the most efficient paths. Any deviations were recorded and analyzed to identify potential areas for improvement.
- Monitoring of Time Spent at Delivery Locations:
- The tags’ 3D accelerometer allowed the system to monitor when delivery personnel were stationary and when they were on the move. The system logged the duration of each stop, providing detailed data on how much time was spent at each delivery location.
- Managers used this data to identify outliers where delivery personnel spent more or less time than expected. This information was critical in standardizing delivery times and reducing delays caused by inefficiencies at individual stops.
- Automated Attendance and Shift Management:
- The depot’s system automatically logged the entry and exit times of delivery staff, efficiently monitoring the beginning and end of their work periods. This automation removed the necessity for manually clocking in and out, decreasing errors and administrative expenses.
- The information was utilized to efficiently organize shifts, guaranteeing that staff adhered to their allotted hours and that overtime was properly monitored and paid for.
Challenges Faced
During the implementation, the company encountered several challenges:
- Initial Resistance from Personnel: Some delivery personnel were initially resistant to carrying the tags, concerned that they might be used for overly intrusive monitoring. To address this, the company held additional meetings to clarify the purpose of the tags, emphasizing that they were tools to improve efficiency and support personnel rather than micromanage them. Over time, as the benefits became clear, resistance diminished.
- Bluetooth Signal Interference: Interference of Bluetooth signals was experienced by the company in densely populated urban areas, impacting the precision of location tracking. The IT team improved the positioning of Bluetooth receivers and refined the system to eliminate interference from unrelated Bluetooth devices, enhancing signal quality and precision.
- Battery Life Management: Although the tags have a long battery life, there were concerns about maintaining consistent operation over extended periods. The company implemented a monitoring system to track battery levels and established a routine for battery checks and replacements, ensuring the tags remained operational without interruption.
Overall, the implementation process was successful, with the company overcoming the initial challenges to fully integrate the i3+ Bluetooth Smart Finder Tags into their delivery operations. The rollout demonstrated the tags’ effectiveness in improving route tracking, time management, and attendance monitoring, laying the foundation for long-term operational improvements.
Data Collection and Analysis
Data Sources
To ensure a comprehensive analysis, data was collected from the following sources:
- Real-Time Tracking Data: The primary data source was the real-time location data generated by the i3+ Bluetooth Smart Finder Tags. This data provided continuous updates on the location and movement of delivery personnel throughout their shifts.
- System Logs: The delivery management system automatically recorded various operational metrics, including route adherence, time spent at each delivery stop, and shift start/end times. These logs served as a critical source of data for analyzing the effectiveness of the tags in streamlining operations.
Feedback from Personnel: Feedback was gathered from the delivery personnel who participated in the case study. This qualitative data provided insights into the practical challenges encountered during implementation and the perceived benefits of the system.
Methodology
The data collected was analyzed using a combination of quantitative and qualitative methods:
- Route Efficiency Analysis:
- Baseline Data: A baseline was established using pre-implementation data to measure route adherence and average delivery times. This baseline served as a point of comparison for the post-implementation data.
- Post-Implementation Data: The real-time tracking data from the i3+ tags was analyzed to measure improvements in route adherence and overall delivery times. Deviations from planned routes were logged and compared against the baseline to determine the effectiveness of the tracking system.
- Time Management Analysis:
- Time at Delivery Locations: The system logs were used to analyze the duration of stops at each delivery location. The data was segmented into different time periods (e.g., peak vs. off-peak hours) to identify patterns and outliers.
- Standardization of Stop Times: The variance in time spent at delivery locations was calculated before and after implementation. A reduction in variance indicated more consistent time management across delivery personnel.
- Attendance Accuracy Analysis:
- Automated Attendance Records: Attendance and shift data from the system logs were compared against manually recorded data (pre-implementation) to assess improvements in accuracy.
- Error Reduction: The frequency and nature of errors in attendance tracking were documented and compared across the two periods. The reduction in errors was used to quantify the impact of automation.
- Qualitative Feedback Analysis:
- Feedback from delivery personnel was categorized based on themes such as usability, perceived impact, and areas for improvement. This feedback was used to contextualize the quantitative findings and identify any additional benefits or challenges.
Key Findings
The analysis revealed several key findings:
- Improved Route Efficiency:
- Route Adherence: The data showed a 12% improvement in route adherence post-implementation. Delivery personnel were more likely to follow optimized routes, reducing unnecessary deviations and improving delivery times by an average of 15%.
- Delivery Time Reduction: The average delivery time per route decreased by 10 minutes, representing a significant increase in overall efficiency.
- Enhanced Time Management at Delivery Locations:
- Reduction in Time Variance: The variance in time spent at delivery stops was reduced by 20%, indicating more consistent performance across delivery personnel. The standardization of stop times contributed to a smoother delivery schedule and fewer delays.
- Identification of Inefficiencies: The analysis identified specific locations where personnel frequently exceeded expected stop times, allowing managers to investigate and address the root causes.
- Increased Attendance Accuracy:
- Error Reduction: The automation of attendance tracking led to a 30% reduction in errors compared to the manual system. This improvement simplified payroll processing and ensured more accurate shift management.
- Shift Compliance: The data showed a 95% compliance rate with scheduled shift times, reducing instances of unauthorized overtime or missed shifts.
- Positive Feedback from Personnel:
- Ease of Use: Most delivery personnel reported that the i3+ tag was easy to use and did not interfere with their daily tasks. They appreciated the reduction in manual reporting and the ability to focus more on their deliveries.
- Perceived Benefits: Personnel noted that the tracking system made their routes more efficient and helped them stay on schedule, reducing the stress of meeting delivery deadlines.
Results and Outcomes
Route Optimization
The implementation of the i3+ Bluetooth Smart Finder Tag led to significant improvements in route optimization:
- Improved Route Adherence: The analysis revealed a 12% increase in route adherence post-implementation. Delivery personnel were more consistent in following the optimized routes provided by the delivery management system. This improvement reduced unnecessary detours and increased overall route efficiency.
- Reduction in Delivery Times: The average delivery time per route decreased by 10 minutes, representing a 15% improvement. This reduction in delivery time was directly correlated with better route adherence and fewer deviations, allowing the company to meet delivery deadlines more consistently.
Metric | Pre-Implementation | Post-Implementation | Improvement |
---|---|---|---|
Route Adherence (%) | 78% | 90% | +12% |
Average Delivery Time (min) | 67 | 57 | -10 min |
Time Management
The deployment of the i3+ tags also positively impacted time management at delivery locations:
- Standardization of Delivery Stops: The variance in time spent at delivery stops was reduced by 20%, leading to more consistent stop times across all delivery personnel. This standardization helped eliminate inefficiencies caused by excessive or insufficient time spent at delivery locations.
- Increased Efficiency: With more consistent stop times, delivery personnel were able to complete their routes more efficiently. This increase in efficiency contributed to the overall reduction in delivery time and improved the company’s ability to maintain a reliable delivery schedule.
Metric | Pre-Implementation | Post-Implementation | Improvement |
---|---|---|---|
Variance in Stop Time (min) | ±8 | ±6 | -20% |
Average Stop Time (min) | 5.2 | 5.0 | -0.2 min |
Attendance and Shift Management
The introduction of automated attendance tracking through the i3+ tags resulted in streamlined processes and reduced errors:
- Reduction in Administrative Errors: The automation of attendance tracking led to a 30% reduction in administrative errors compared to the manual system. This improvement simplified payroll processing and made shift management more accurate and reliable.
- Enhanced Shift Compliance: The compliance rate with scheduled shift times improved to 95%, indicating that delivery personnel were consistently starting and ending their shifts on time. This improvement reduced unauthorized overtime and ensured better alignment with operational schedules.
Metric | Pre-Implementation | Post-Implementation | Improvement |
---|---|---|---|
Attendance Error Rate (%) | 10% | 7% | -30% |
Shift Compliance Rate (%) | 85% | 95% | +10% |
These results clearly demonstrate the positive impact of the i3+ Bluetooth Smart Finder Tag on the company’s delivery operations. The improvements in route optimization, time management, and attendance tracking have not only enhanced operational efficiency but also contributed to a more streamlined and reliable delivery process.
Discussion
Analysis of How the i3+ Tag Contributed to Solving the Identified Problems
The implementation of the i3+ Bluetooth Smart Finder Tag effectively addressed the three primary challenges identified at the beginning of this case study: tracking delivery personnel, managing time spent at delivery locations, and automating attendance and shift management.
- Tracking Delivery Personnel on Their Routes:
- The i3+ tag’s real-time location tracking capabilities provided managers with precise, up-to-date information on the whereabouts of delivery personnel. This improved route adherence by 12%, allowing managers to ensure that delivery routes were followed more consistently. The result was a 15% reduction in average delivery times, directly addressing the inefficiencies caused by route deviations.
- Managing Time Spent at Delivery Locations:
- By utilizing the tag’s 3D accelerometer, the system could accurately monitor the time delivery personnel spent at each stop. The reduction in time variance by 20% standardized the delivery process, reducing the occurrence of delays caused by excessive or insufficient time spent at delivery locations. This standardization contributed to a smoother overall delivery schedule.
- Automating Attendance and Shift Management:
- The automated attendance tracking provided by the i3+ tag led to a significant reduction in administrative errors (30%) and improved shift compliance by 10%. This automation reduced the manual workload for managers and ensured that delivery personnel were consistently starting and ending their shifts on time, improving overall operational efficiency.
Comparison of Pre- and Post-Implementation Performance
The comparison of pre- and post-implementation data highlights the effectiveness of the i3+ tag in addressing the company’s operational challenges:
- Route Efficiency: Pre-implementation, route adherence was inconsistent, with frequent deviations leading to delays. Post-implementation, route adherence improved by 12%, resulting in more predictable delivery times and a 10-minute reduction in average delivery times.
- Time Management: Before implementing the i3+ tags, there was significant variability in the time spent at delivery locations, contributing to inefficiencies. Post-implementation, this variance was reduced by 20%, leading to more consistent and efficient delivery operations.
Attendance Accuracy: Manual attendance tracking was prone to errors, leading to discrepancies in payroll and shift management. The automation provided by the i3+ tags reduced these errors by 30% and improved shift compliance, ensuring better alignment with operational schedules.
Unexpected Outcomes or Additional Benefits Realized
In addition to the anticipated improvements, the study revealed several unexpected outcomes and additional benefits:
- Enhanced Accountability: The visibility provided by the i3+ tag increased accountability among delivery personnel. Knowing that their location and time at stops were being tracked encouraged more disciplined behavior, further contributing to operational efficiency.
- Improved Communication: The real-time tracking data enabled quicker communication between managers and delivery personnel. If a delivery was delayed or a route deviation occurred, managers could proactively address the issue by communicating directly with the personnel involved.
Positive Personnel Feedback: Initially, there was some resistance to the implementation of the tags. However, as delivery personnel experienced the benefits—such as less manual reporting and more streamlined routes—their feedback became increasingly positive. They reported feeling more supported and less stressed about meeting delivery deadlines.
Challenges and Limitations of the Study
Despite the overall success of the implementation, several challenges and limitations were encountered:
- Initial Resistance: As mentioned, some delivery personnel were initially resistant to carrying the i3+ tags, perceiving them as tools for micromanagement. This resistance required additional communication and training to overcome.
- Bluetooth Signal Interference: In urban areas with high-density Bluetooth devices, signal interference occasionally affected the accuracy of the tracking data. Although mitigated through system adjustments, this remains a potential limitation in highly congested areas.
- Battery Management: While the tags boast a long battery life, monitoring battery levels and ensuring timely replacements posed an ongoing challenge. Establishing a routine for battery checks helped address this, but it introduced an additional maintenance task.
- Sample Size: The study was conducted with a limited sample size of 20 delivery personnel. While the results are promising, scaling up the implementation across the entire delivery fleet may present new challenges that were not encountered in this smaller study.
Conclusion
Recap of the Main Findings
The implementation of the i3+ Bluetooth Smart Finder Tag addressed several critical operational challenges faced by the delivery company. The key findings from the case study include:
- Improved Route Efficiency: The introduction of real-time tracking led to a 12% improvement in route adherence and a 15% reduction in average delivery times.
- Enhanced Time Management: The standardization of time spent at delivery locations resulted in a 20% reduction in time variance, contributing to more consistent and efficient delivery schedules.
- Streamlined Attendance and Shift Management: The automation of attendance tracking reduced administrative errors by 30% and improved shift compliance by 10%, simplifying payroll processing and shift management.
The Overall Impact of the i3+ Bluetooth Smart Finder Tag on Delivery Operations
The deployment of the i3+ Bluetooth Smart Finder Tag significantly enhanced the company’s delivery operations. The tag’s real-time tracking capabilities, coupled with its ability to monitor time spent at delivery locations and automate attendance management, led to measurable improvements in efficiency, accuracy, and overall operational performance. The company experienced smoother delivery processes, more predictable delivery times, and a reduction in manual administrative tasks, all of which contributed to higher levels of customer satisfaction and better utilization of resources.
The positive feedback from delivery personnel and the reduction in operational inefficiencies underscore the value of the i3+ tag as a tool for improving logistics management. The data-driven insights gained from the system enabled the company to make informed decisions, optimize routes, and address inefficiencies that previously hindered performance.
Long-Term Benefits and Potential for Further Scale-Up
The long-term benefits of implementing the i3+ Bluetooth Smart Finder Tag are clear. The solution not only addresses immediate operational challenges but also lays the foundation for continued improvement in delivery performance. As the company scales up the use of the i3+ tags across its entire delivery fleet, the following benefits are anticipated:
- Scalability: The system’s success with a small sample of delivery personnel suggests it can be effectively scaled to cover the entire fleet, leading to even greater efficiency gains.
- Data-Driven Optimization: As more data is collected, the company can further refine delivery routes, optimize time management, and enhance shift planning. The continuous feedback loop will support ongoing improvements.
- Future Integration: The i3+ tags could be integrated with other smart technologies, such as predictive analytics or AI-driven route optimization, to further enhance operational capabilities.
In conclusion, the i3+ Bluetooth Smart Finder Tag has proven to be a valuable asset in transforming the company’s delivery operations. Its successful implementation has demonstrated tangible improvements in route efficiency, time management, and attendance accuracy, paving the way for long-term benefits and potential expansion. The company is well-positioned to build on this success, leveraging the insights gained from the case study to achieve greater operational excellence in the future.